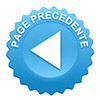
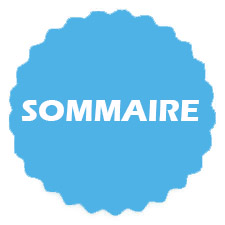
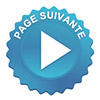
2.5 ESSAIS DE FATIGUE OU D'ENDURANCE
2.5.1 Phénomène de fatigue
Il est de première importance pour les structures d'avions et dans d'autres domaines comme l'automobile par exemple ou une bielle de moteur est sollicitée alternativement à la compression et à la traction de ± 60 cycles par seconde. Une roue d'automobile mal équilibrée est aussi un exemple de système soumis à un phénomène de fatigue. Un effet de
résonance peut l'amplifier, la rupture peut se produire produire après un certain nombre de cycle ou aller et retour, retour, sous des efforts bien inférieurs aux limites usuelles du matériau ( Rr ou Re ). usuelles du matériau ( Rr ou Re ) Une telle rupture est dite rupture est dite par fatigue et ce phénomène se déroule en 3 phases distinctes. phases distinctes.
1. Phase d'initiation de la fissure : Il y a formation d'une microfissure( Fig. 2-18) : C'est la germination ou l'amorçage de la fissure. Cette phase de formation peut représenter 80 à 98%
de la durée de vie d'une pièce de structure au sens général du terme ( dans notre exemple : Un arbre de transmission ).
Toute discontinuité de surface favorise cette germination ( exemples : Piqûres de corrosion, entailles, congés de raccordement à angle droit, usinages, inclusions de surface, etc . ). Cette première phase est cependant réversible, la pièce peut être réparée par un traitement thermique ( recuit, etc. ) ou mécanique.
2. Phase de propagation de la fissure : Après amorce, la fissures s'agrandit sous l'action des efforts alternés qui écartent ou rapprochent continuellement les parties fissurées ; il y a un phénomène de concentration de contraintes en ces points.
3. Phase de rupture finale de la pièce : La rupture définitive se produit brutalement lorsque les dimensions de la partie non encore fissurée ne sont plus suffisantes pour supporter les charges exercées.
2.5.2 Essai de fatigue
Les résultats des essais statistiques sont statistiques dans la mesure où des éprouvettes identiques, sous les mêmes conditions d'essai, donnent des résultats différents. Cette valeur moyenne, une fois déterminée est choisie comme représentative de la capacité du matériau ( analogie avec la durée de vie des roulements ).
Il y a trois types d'essais de fatigue : traction - compression ; torsion alternée et flexion alternée ( le plus classique ) et flexion pure alternée. Considérons une barre en acier encastrée rigidement en A et sollicitée à son extrémité B par un système bielle-manivelle ( Fig. 2-19). Bien que les phénomènes de flexion n'ont pas encore été étudiés, on peut concevoir que la section dangereuse de cette barre est située en A ( encastrement ), que la contrainte en ce point sera plus importante si l'on impose en B un déplacement plus grand.
En A1 on constate une contrainte de traction lorsque la force F est dirigée vers le bas et en A2 on constate une contrainte de compression . et nous aurons l'effet inverse lorsque la force sera dirigée vers le haut. Ce fixer la valeur de f ( alternativement positive et négative ), c'est s'imposer en certains points de la barre des contraintes égales et connues de compression et traction. L'essai de fatigue montre que pour une contrainte alternée donnée, la rupture de la barre se produit après un certain nombre de tours de manivelle, donc d'alternances.
Exemples : Supposons une barre en acier de construction C32 trempé + revenu. Sous une contrainte alternée de 430 N/mm², la rupture se produit au bout de
Si la contrainte alternée ( soit f et -f ) imposée à la barre est réduite, la rupture se produira, mais après un plus grand nombre d'alternance. Ex.
2.5.3 Détection des déformations
1. Les vernis craquelants : Ils sont projetés sur la surface à étudier comme un aérosol et utilisés pour localiser visuellement les zones les plus chargées afin de pouvoir marquer les directions principales des déformations. Ils permettent de choisir les emplacements de pose des jauges de contraintes et leur orientation, celle-ci étant toujours perpendiculaires à la direction de la déformation en traction la plus importante.
2. Méthode photoélastique: Cette méthode est plus précise que celle des vernis craquelants et permet des études plus détaillées sur les zones les plus chargées comme par exemple les directions principales des déformations. Les résultats obtenus sont particulièrement intéressants près des formes amenant des concentrations de contraintes ( trous, encoches, épaulements , . )
Une matière plastique transparente est utilisée pour modéliser l'objet réel. Un système optique spécial ( polariscope ) permet d'observer des motifs colorés, interpréter et visualiser les zones de contraintes. Il est aussi possible, par dessins et essais successifs, d'améliorer la définition des objets. Les pièces soumises à des vibrations ou à des charges dynamiques peuvent être étudiées avec un système stroboscopique. L'étude dans les trois dimensions est envisageable par tranches découpées dans des modèles 3D " figés ".
3. Extensomètrie électrique
a) Principe : L'extensomètrie électrique est basée sur basée sur l'emploi des jauges de contraintes. C'est la méthode expérimentale la plus usuelle permettant de vérifier les résultats théoriques ( calculs des contraintes, de déformations, .. ). Les jauges sont collées sur la surface à étudier et mesurent les déformations en un point donné. La déformation subie est transformée en variation de résistance électrique mesurée par un pont d'extensomètrie, c'est en fait le même principe que le pont de Wheatstone. Les contraintes sont ensuite obtenues par calcul à partir des lois de la résistance des matériaux et de l'élasticité.
b) Essai : Sous l'effet d'un allongement, la section du brin ( fil ) de la jauge diminue, il en résulte une variation de la résistance électrique du fil. En mesure, la jauge active R1 est collée sur la structure et une jauge identique R2 est collée sur une pièce de même matière. R2 ne subit aucune contrainte et est à la même température que R1. Dans certains capteurs ( forces, pressions, couples, déplacement, . ) on utilise généralement quatre jauges judicieusement disposées. Il est souvent impossible de décoller les jauges sans les détériorer, ce qui fait grimper le prix des essais.
Les jauges sont souvent fabriquées de la même manière que les circuits imprimés et sont disponibles sous plusieurs formes et dans de nombreuses dimensions.
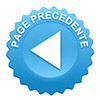
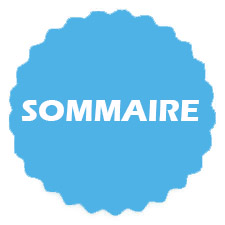
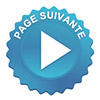
Dernière édition: